Condensing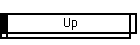
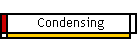
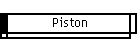
| |
Condensation, where & when
it happens is very important. It's the reason for the efficiency advantage of STS over ORC-Turbines.
The key difference between the STS Organic Rankine Cycle and conventional turbine engines has to do with the limits
of expansion of the vapor. We're down to the wire here. The theories are really the same. The physics
is the same, the equations, the pieces and parts, boiler, condenser, liquid pumps... everything except the expansion
device and and the controller behind it, and of course the Safe Operating Area (SOA). SOA refers to the maximum
set of conditions that a device may operate under, for an electronic device like a transistor, it refers to the the
limits of voltage, current, power and temperature that the Device Under Test (DUT) may be exposed to then the others are
known or controlled. Naturally you can't expose the DUT to max voltage and max current at the same time, because
that would exceed the max power specification. And you can't expose it to max power when it's at max temperature,
because it will burn up. Once you grasp the concept of SOA, it's an excellent tool.
The advantage of the STS ORC-Piston over the ORC-Turbine is based in the SOA. A critical SOA criterion for the
ORC-Turbine is in the Quality (Q%) of the exhaust stream. The turbine must maintain a fairly high minimum Q% or
the blades and stators will be destroyed. The STS piston is virtually immune to this factor. This is what
allows the STS to extract more energy from each unit of mass flow at any given starting temperature.
The advantage lies in the way the systems compare & contrast.
Turbine designers know that the best solution from the energy standpoint is maximum expansion of the gas, even to
cryogenic temperatures, but the inability of the materials to operate/survive in those conditions has resulted in the
standard compromise. Turbines are capable of large ratios, but are limited by the physical phenomenon of condensation.
Condensation will always occur when the energy extracted from a gas causes its temperature to fall. As the
gas/vapor passes thru its saturation temperature at the prevailing pressure, droplets of liquid form, this fog no longer
exhibits the flow characteristics of a gas in the turbine. The high speed blades impinge on the liquid droplets, and
this causes erosion of the turbine components. Turbine operators and designers have observed and understood this since
the early days, and have taken steps to eliminate the "problem".
|
Piston engine designers also know that the key to performance and efficiency is found in high
compression/expansion ratios. Although high ratios are somewhat harder to obtain in piston engines than they are in
turbines, the STS designs boast 78:1 in a small 1''x1'' bore x stroke model, rising to almost 400:1 in a 4'' x 4''
engine. Obviously these ratios are not the result of simply rearranging an IC engine or gas compressor. The STS designed
valves; their drive, control and arrangement are the key to achieving these unique results. Just like the turbine, the
expansion results in condensation at the expense of energy in the gas. This energy becomes the work that the engine
delivers to the load. Unlike the turbine, the piston is not harmed by the mist/fog in the cylinder. At the point of
maximum condensation the piston is near BDC of its stroke and essentially not moving; no motion = no erosion.
|
As the wet vapor leaves the cylinder there exists an opportunity to capture the deviation from
equilibrium. The ultimate heat sink for the process is the atmosphere, and
while the “gas” must be re-heated to above atmospheric temperature to reject the final portion of the unavailable
energy it contains; the liquid need not. At this moment, the system can realize the gain made in the
cylinder. By separating the liquid from the gas, we can re compress a smaller mass fraction than we extracted
energy from and therefore reject a smaller fraction of the gross-energy input.
It might be assumed at this point that we are proposing to violate Carnot! This
is certainly not the case. The Carnot efficiency depends on the temperature difference.
By splitting the mass stream into two components, we are removing some of the energy of the stream at a far lower
temperature than the temperature of the heat-sink, but this is an unstable or non-equilibrium state, the liquid and gas
would return to a mean temperature above atmospheric, if they were allowed to do so. It is only by exploiting this lag in the equilibrium that we obtain the advantage.
|
| |
...............
...............
|